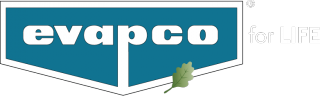
Closed Circuit Coolers: Design with winter in mind
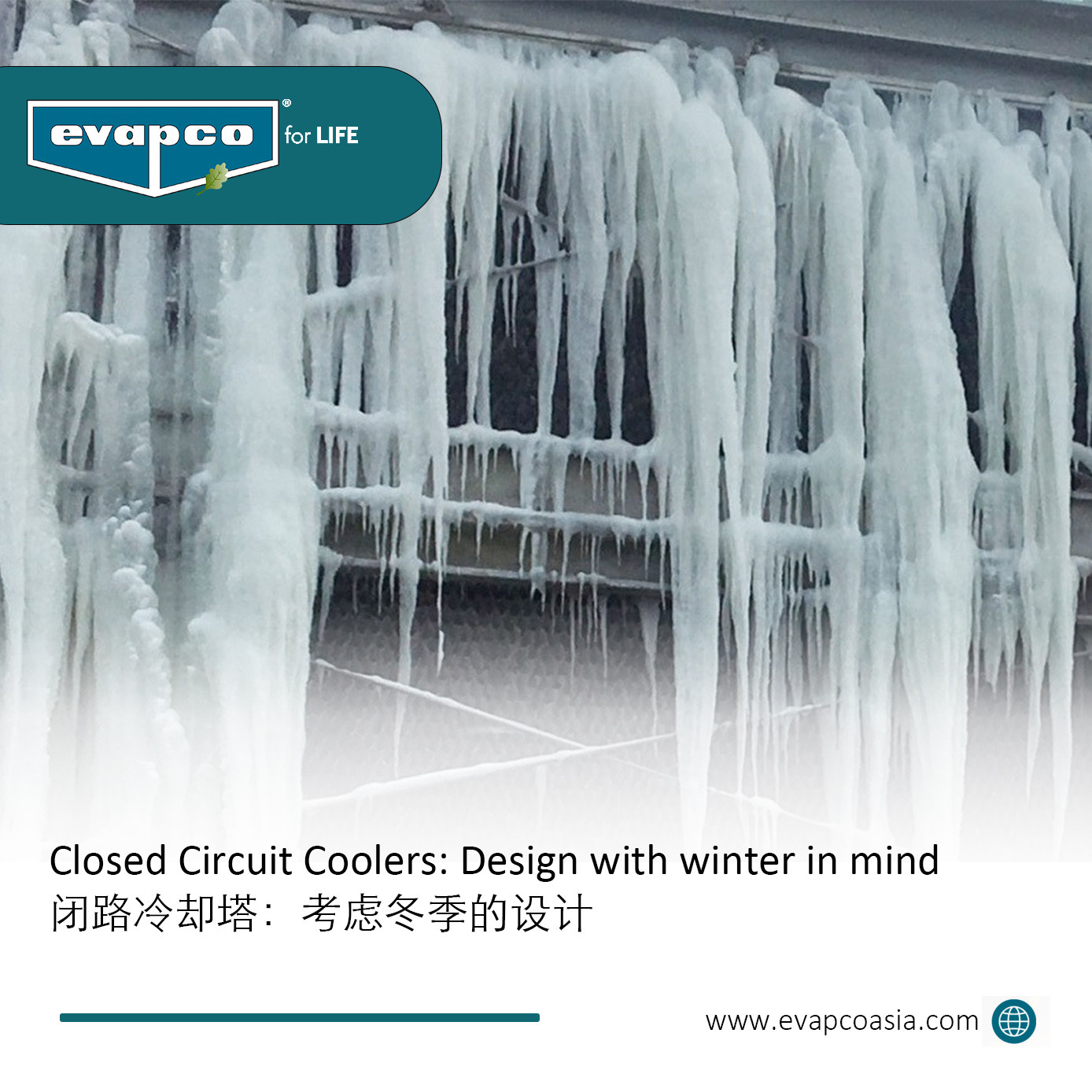
When outside temperatures fall below freezing, water inevitably forms into ice. Open cooling towers can be susceptible to freezing due to their inherent nature of operation. As a result, ice formation becomes a subject of management, not elimination. Fortunately, there are alternative solutions.
Closed circuit coolers are used for a lot of specialized applications, and are ideal for evaporative cooling applications in severe winter climates. If ice formation is not managed properly, expect to see reduced thermal performance, part failures, and additional field maintenance. Make sure that your closed circuit cooler is designed, specified, and built with winter in mind.
Selection:
• For the ideal solution, select a closed circuit cooler with finned coils. This will increase your ambient dry bulb switchover temperature and allow the closed circuit cooler to run dry (spray pump off) for the maximum amount of hours during the spring, fall and winter.
• Select a closed circuit cooler for optimum free cooling operation. Winter cooling conditions are typically more difficult to achieve than summer conditions and therefore should be the basis for equipment selection.
• Implement an automatic draining system for the cold water basin when operating dry for extended periods of time. This will eliminate unnecessary and excessive operation of the electric basin heaters.
Process Fluid:
• Depending on your climate, utilize a solution of ethylene or propylene glycol in order to protect the process fluid during freezing conditions.
• Remember glycol is less efficient at transferring heat then water. Factoring in derates is imperative while optimizing for the unit’s capacity.
• Fluid in motion is less susceptible to freezing. Adhere to the manufacturer’s recommendations for minimum flow rates for freeze protection, especially when the process fluid is water.
• A 30% solution of ethylene or propylene glycol protects the process fluid from freezing down to 6.7°F (-14°C) and 9.2°F (-12.7°C) when crystallization begins. The burst point of these two solutions is not until -60°F (-51°C)!
Accessories:
• Add a discharge hood with dampers and insulation to the casing section when the coil is located in the air stream to reduce heat loss. As an additional measure add insulation to the discharge hood with dampers.
• Mechanical float valves are located inside of the unit and cannot be heat traced, leaving the valve susceptible to freezing. Substitute the float assemblies with an electronic water level control, and utilize an external solenoid valve which can be heat traced and insulated.
• Add a heater package in order to keep your basin water from freezing. Size the heaters based on extreme ambient temperatures. Heaters are designed to maintain 40°F basin water temperatures.
• Ice formation can occur on fan blades when inclement weather conditions present themselves. Include a vibration cut out switch to detect excessive vibration and shut down the fan motor before extreme damage can occur.
• Include a “de-icing” control sequence which reverses fan direction for a set period of time. This technique will assist in ice management.
Learn more about EVAPCO coolers or contact your local EVAPCO Sales Representative.